Nolan: Début 70...
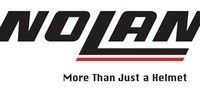
« Mon accident de 1983 : moi, Gardner et mon casque Nolan. Je tombe. Gardner me percute et Nolan me sauve la vie. Merci Nolan » a déclaré Franco Uncini… ex-champion du Monde 500 cc.
Nolan, marque italienne de casque qui a fêté ses 35 ans d'existence en 2007, a été portée par les plus grands pilotes aux fils des saisons.
Entre procédés innovants, casques de toutes gammes, philosophie racing et control total et direct du cycle productif, le groupe Nolan a su s'imposer dans le monde du casque deux roues… voici son histoire.
1972, Lander Nocchi, entrepreneur dans le secteur des accessoires auto et moto de son état, a un projet ambitieux : créer des casques plus légers et moins chers par rapport à ce qui se faisait à l'époque… Nolan voit le jour.
LE PLASTIQUE C'EST FANTASTIQUE…
Lander Nocchi importe des Etats-Unis un matériau léger et novateur pour l'époque : le Lexan. Après l'achat de presses, l'entrepreneur italien installe son usine dans la petite ville de Brembate di Sopra, près de Bergame, au nord de Milan… Nolan voit le jour.
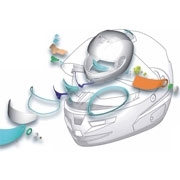
Aujourd'hui, même si l'usine n'a pas changé de place, elle a pris, comment dire… un peu plus d'ampleur : la marque est distribuée dans plus de 70 pays à travers le monde, elle compte plus de 350 employés qui produisent plus d'un million de casques Nolan, X-lite et Grex chaque année.
Chauffé à pratiquement 300°C, le Lexan liquide est injecté dans un moule à 2 parties sous pression. Toutes les 80 secondes, une coque est créée.
MADE IN NOLAN
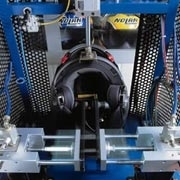
- Lors des tests de résistance aux chocs, la coque externe moulée en polycarbonate Lexan a enregistré des valeurs max de 900/ 1000 J/m par rapport aux valeurs (toujours maximales) de 550/ 600 J/ m de la résine ABS. Cette résine se distingue également par sa résistance thermique : la plage s'étend de -30°C à +120°C contre -20°C à +50°C pour l'ABS.
Nolan effectue des tests sur les calottes vernies ou non à température ambiante ou à -20°C. Le test prévoit la solidité de l'échantillon via un projectile lancé avec une énergie de 400 joules sur des points d'impacts spécifiques.
- Peinte à l'eau, la coque reçoit une finition protectrice Hi-Brite garantissant un brillant de la couleur sur du long terme.
Le vernissage, quant à lui est testé dans une chambre thermique spécifique à l'intérieur de laquelle les calottes sont conditionnées avec des cycles spécifiques de 15 heures avec une humidité relative allant de 10% à 75% et une température variant entre 40 et 80°C. Pour vérifier les décalcomanies, un test est effectué à 100°C permettant de vérifier qu'elles sont bien appropriées dans toutes les conditions…
- La coque interne est moulée par injection en polystyrène expansé. Elle est produite avec différents degrés de densité (mono ou double) pour optimiser ses performances.
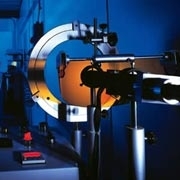
- L'écran est moulé par injection en résine Lexan offrant une protection UV jusqu'à 400 nanomètres.
Afin d'être aux normes européennes, ils doivent garantir une transmission lumineuse supérieure à 80%. Une transmission supérieure à 50% peut être acceptée (écran fumé) à condition que l'inscription « Daytime use only » (utilisation diurne uniquement) figure sur l'écran.
Ceux dont la transmission lumineuse est inférieure (écran fumé foncé) sont faits pour être utilisés uniquement sur circuit… en théorie…
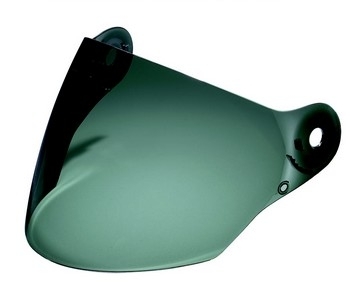
- Les mousses internes de conforts (pour tous casque Nolan et X-lite) sont soumises à un traitement respirant et anallergique (Sanitized) pour assurer un bon niveau de confort. Pour rester sur le même registre, Nolan réalise sur ses mousses une thermo-soudure permettant de remplacer partiellement les coutures traditionnelles…
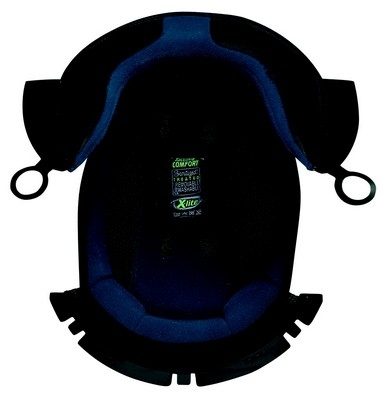
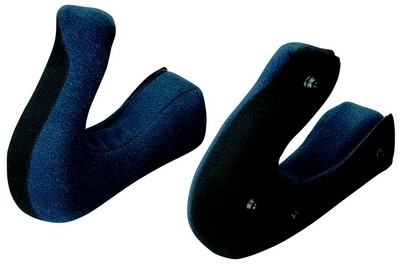
Sommaire
Déposer un commentaire
Alerte de modération
Alerte de modération